Author

Design and Engineering Challenges for Panel Manufacturers
Today's product development process (PDP) can usually only be carried out efficiently with the aid of software-based systems. A multitude of different software systems are available, but good software is usually restricted to specific rather than general applications and this can create problems of its own! In this blog we'll be exploring the design challenges (and possible solutions) for panel manufacturers.
Discover how the design and manufacture of control cabinets can be made easier and more efficient.
A possible solution is to adopt one of the many widely available CAD systems. Traditionally, these were designed for architects and mechanical engineers and in these applications they can give good service. However, they typically lack costing and ordering functions - which are essential for panel manufacturers. Users of traditional CAD systems often address this shortcoming by using separate software solutions for costing and ordering.
Using different software systems for the different phases of control cabinet manufacturer is, however, far from ideal as it is usually difficult to pass data between the systems. In fact, this may end up being a manual task, which is not only time consuming but also prone to error.
Using multiple software systems creates obstacles not only in engineering but in production, where inefficient or incomplete data transfer to and from the shop floor systems can lead to mistakes that are difficult and costly to rectify. The solution is the use of single-source software that covers all of the functions needed for efficient design, component sourcing and manufacturing, and also supports 3D modelling of virtual control cabinets and switchgear - an approach which is both fast and intuitive.
Software features for the design engineer should include interactive 3D mounting layout and wiring functions, along with the provision for the design of busbar systems. Further aids such as collision testing, enforced adherence to component manufacturer's installation guidelines, minimum clearances and bending radii, also aid the design process and minimise the risk of mistakes.
Designers who adopt a functional-unit approach when using an integrated computer-aided engineering (CAE) system will see even greater cost-reduction and productivity benefits. Of course, many panel manufacturers argue that, because of diversity of the work they carry out, functional units would be difficult or impossible for them to adopt. There is good evidence that they should think again!
A well-chosen CAE supplier will provide all of the expert guidance needed for companies to adopt functional engineering, and the rewards are great. Control panel manufacturers who are already working in this way, thereby enabling the use of (online) configurators, report that up to 44% savings in time and costs are possible, which translates to a very large competitive advantage.
If all of this sounds interesting, why not find out more? Simply download EPLAN's new whitepaper, which specifically addresses the challenges and needs of panel manufacturers and is packed with practical ideas and information.
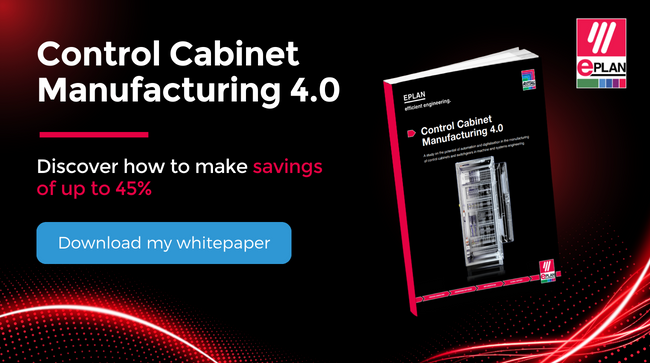
Comments