Author

Engineering 4.0 brings efficiency at your fingertips
A recent study evaluating the use of CAE software – of which EPLAN products are leading examples – revealed that engineering companies could typically achieve time savings of 25%, and sometimes as much as 50%, by partially automating engineering processes. In other words, with a relatively modest investment, manufacturers can reap serious benefits.
The European 4.0 Transformation Centre (E4TC) at the RWTH Aachen University Campus investigated the strategic digitalisation of the design and control of machines and factories. A recent eight-month field study carried out by E4TC examined a total of ten process steps for engineering in machine manufacturing and created a workflow model that contains the typical work steps of the production cycle: engineering, design, bills of materials, reports, control cabinet layout, devices and templates.
The path to higher efficiencies in the value chain was mapped out using established methods, going from standardisation through to automation. To evaluate the efficiency of each work step, the study examined the workflow methodology at five different “eLevels”.
One important conclusion was that standardisation of devices and design templates (equivalent to moving to eLevel3) can save 50 percent of the time required to create schematic diagrams. What’s more, by going further and moving to partial automation (eLevel4), an additional 25 percent of the time can be saved.
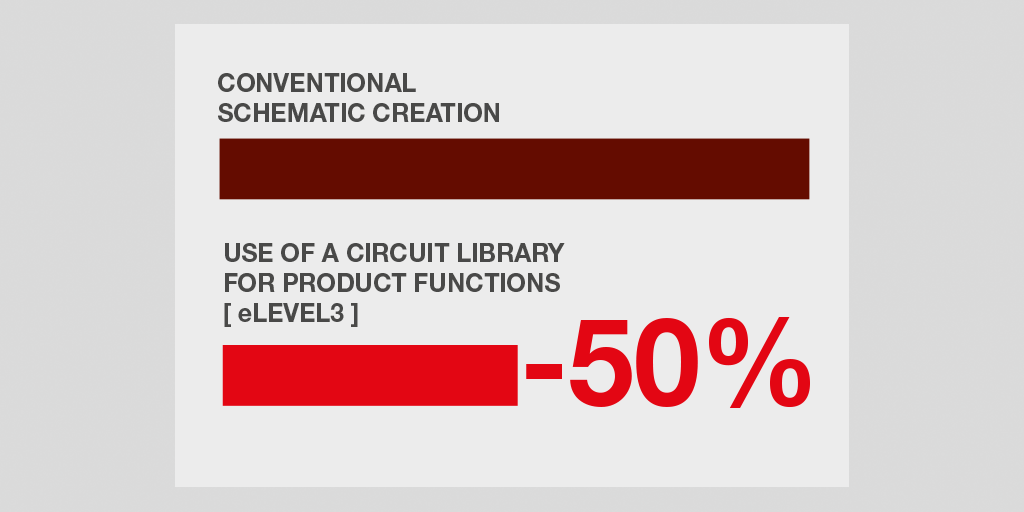
Using the data they collected, the researchers found that that engineering companies can become 20% more efficient by moving from one eLevel to the next eLevel, and that device-oriented working methods bring a 25% time saving for schematic creation. These time savings, which result from the use of CAE systems, translate into cost reductions that can significantly enhance profitability. The study further showed that the key to higher efficiency in engineering lies in the division of labour into order processing and data generation for standardisation.
Comprehensive digital engineering documents that include schematics and 3D control cabinet designs – known as digital twins – enable considerable optimisation in manufacturing. This potential is very well illustrated in the document “Control Cabinet Manufacturing 4.0” from the Institute for Control Engineering of Machine Tools and Manufacturing Units (ISW) at the University of Stuttgart.
To help customers achieve the benefits promised by Industry 4.0, EPLAN offers a portfolio of solutions that comprise the core elements for digitalisation. With scalable processes, companies can invest in Industry 4.0 to become completely and comprehensively digitalised across the entire value chain. This way, they can move to an Engineering 4.0-ready manufacturing environment that delivers efficiencies, saves money and improves their ecological credentials.
If you would like to apply this philosophy in your own company, simply download our report, which is free of charge, and you’ll have the key insights at your fingertips.
Comments