Author

NorthWind Technical Services, LLC: Efficient Engineering with EPLAN & Rittal
Synopsis
NorthWind recognises that automation is the heart and soul of every modern manufacturing system. In today’s competitive environment, every system and every customer is unique and requires attention to individual details and needs. This has always been NorthWind’s strongest point - everything they do is 100% customer focused. Likewise, NorthWind has been careful to choose industry partners that have the same commitment to ensuring their customer’s success.
NorthWind has been working to automate and streamline the entire process of designing, building and programming control systems since 2005. This effort has resulted in the development of the NorthWind PlantLOGIX™ suite of software.
"The new software and machinery have resulted in a drastic reduction in schematics creation time, increased design quality, decreased shop build time by 50% and increased quote accuracy to customers." Mike Bosworth |
This includes QuikLOGIX®, a software tool that speeds up and standardises PLC programming and HMI configuration, connecting all this information to the electrical schematics. This ability to connect schematics to the rest of the design process was not possible until a partnership with EPLAN was established in 2011. EPLAN’s database centric architecture fit perfectly with NorthWind’s design and programming needs.
In 2017 NorthWind sought to extend its Automated Development Process (ADP) established for design and programming to the shop floor. NorthWind turned to EPLAN again along with EPLAN’s sister company, Rittal, for help. They responded with EPLAN Engineering Configuration (EEC One), a Rittal Perforex cutting machine, and a Wire Terminal (WT) wiring machine. Together these technologies (software and equipment) now allow NorthWind to extend their ADP all the way through the control panel manufacturing process.
This system maximises beneficial impacts for customers by creating a design and manufacturing process with repeatable results in less time and with lower cost. This partnership has resulted in:
|
Challenges
NorthWind experienced many challenges related to manual manufacturing processes and human error prior to the implementation of EEC One, and the Perforex and WT machines into their workflow. “We had multiple projects that were over-quoted hours on design and shop build time,” according to Benjamin Drew, Project Manager in charge of NorthWind’s Design Team.
"Our most valuable resources were spinning their wheels saving business relations when they should have been focused on new progressive endeavors." Matt Bosworth VP of Manufacturing NorthWind |
Projects were completed manually, and some of the traditional methods they relied on had become outdated, putting the company at risk of being outpaced by their competition. Production tasks like drilling, cutting and crimping often resulted in wasted materials when mistakes were made. This waste can be difficult to spot right away but it adds up when you see how often reorders take place.
There were also many hours wasted re-typing information that is procured in the drawing phase and while writing PLC and HMI programs. Human error resulted in mistyped tags and ID numbers. Changes in any design information and all the places that it needed updating also added to the time requirement for system design and programming. In addition to costs and time, NorthWind noticed that some of their tenured engineers were focusing efforts on triage for projects that were running over original scope of work. “Our most valuable resources were spinning their wheels saving business relations when they should have been focused on new progressive endeavors,” said Matt Bosworth, VP of Manufacturing.
Executive Summary
“We’ve been using EPLAN software for quite some time now and have implemented new practices at various stages that have saved time. When we implemented EPLAN Engineering Configuration (EEC One), we saw a drastic reduction in schematic creation time. Since we implemented a Perforex machine in 2017 and Wire Terminal machine in 2019, we have reduced shop build time to less than half of what it was before.”
As a measure of success,where projects that were over-quoted hours on design and shop build time, NorthWind now has reduced both to where they are typically under on project hours with better quality designs.
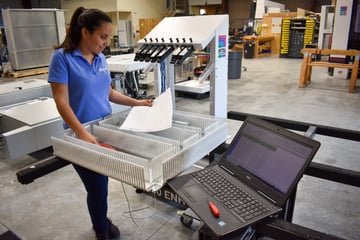
Integration at all levels of the project is the biggest advantage NorthWind has seen. “We chose EPLAN because it is a database-centric product” said Michael Bosworth, President of NorthWind. “This allowed us to connect our schematics to our PLC and HMI programs using NorthWind’s own QuikLOGIX® tool. The result is that NorthWind has one common database that ties our systems together starting with the P&ID through the schematics, panel fabrication and all the way to the PLC & HMI programs. We can do exports to the shop for wire labels and tags to make them match exactly with what is represented in EPLAN. We can also interact directly with the programming software linking I/O and descriptions to the devices. This efficiency eliminates much busy work and the errors that can result from having to retype this information. We always strive to make our own processes more accurate and more efficient. EPLAN strives for these same goals, making for a great partnership!” according to Mike Bosworth.
A typical project consists of Electrical Design, PLC Programming, HMI Configuration, Panel Design, Panel Build and Electrical Installation. When an order is received, the Design Team kicks off the Automated Development Process in the electrical design phase. Since the drawing set created during this phase is used throughout the rest of the project, it is a very critical component of every project.
The designs are exported to the Rittal Perforex Machine for exact placement of all panel cutouts, and the back panel is pre-drilled allowing the panel to be quickly assembled. From there the drawings are sent through the WT-36 wiring machine where the wire specifications drive all cutting, striping, labeling and ferruling of the wires. Panel Technicians then use the
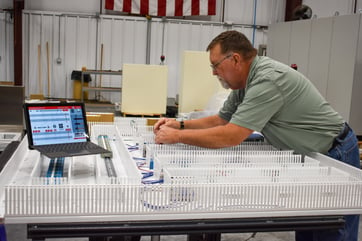
EPLAN Smart Wiring software to guide them through the wiring process. The electrical drawings also connect to NorthWind’s QuikLOGIX® programming software linking the I/O and device descriptions. This connection also reduces errors while speeding the programming process up.
Results, Return on Investment and Future Plans
As a result of its partnership with EPLAN and Rittal, NorthWind is seeing many benefits for themselves and their customers. According to Mike Bosworth, “Our ability to reach our ADP goal has been aided greatly by EPLAN and Rittal. Each step in this process, using software and services supplied by these companies and our NorthWind PlantLOGIX™ suite of software, has allowed us to automate our own processes so that we can serve our customers better and faster. The new software and machinery have resulted in a drastic reduction in schematics creation time, increased design quality, decreased shop build time by 50% and increased quote accuracy to customers. Because we’ve been able to reach our goals with their support, we will continue to work with Rittal and EPLAN to discover new ways to make our business run with greater efficiency.”
Discover more about this joint EPLAN and Rittal partnership and how this could benefit your whole value chain in the new 'Next Level for Industry':
Do you also work in the panel building industry? Check out the new animation and discover for yourself which EPLAN solutions can improve your processes; from sourcing and engineering, through to panel modification and wiring.
Click the image to view.
Comments